Plastics & Elastomers
Thousands of materials. Hundreds of suppliers. Find all the information you need to develop safer, sustainable products faster than ever before. You'll also benefit from our decades of industry experience and strong relationships. And Prospector integrates more than 45,000 UL plastics registration Yellow Cards, providing you direct access to invaluable data on UL-rated materials.
Register TodayExplore Prospector's in-depth technical data.
Find UL Yellow Cards

UL's Yellow Cards are a globally recognized safety and quality guarantee, a certified demonstration of how plastics have met a specific set of performance credentials.
Browse Datasheets
Prospector offers detailed datasheets for thousands of products. Find what you need,browsing by product or supplier name:
Explore Generic Families
When you have a concept of the kind of material you need, start with the generic family thensearch by application or feature:
Data for Engineers and Product Developers
Create your free account to leverage the Prospector database to find the materials and technical data you need to speed the product development cycle. Analyze technical data on more than 100,000 resin and plastic materials. Contact any of the hundreds of global suppliers and distributors directly for pricing and sourcing.
Find solutions, not just materials.
Register TodayLooking for even more plastics content?
Get more out of Prospector's in-depth plastics knowledge with an upgraded plan
Refine your material search with filters specific to your project. With more than 600 properties, you can build your search to your exact specificity.
Evaluate the properties of up to five materials side-by-side to find the best fit for your durability, flexibility, thermal or sustainability needs.
Alternative resin search helps you find replacement materials for discontinued products, lower cost offsets, or switch to a better-performing plastic in minutes.
Searchable curve data guides you in selecting an appropriate material by mechanical behavior under various stresses and strains.
INDUSTRY WEBINARS Find more webinars
Benefit from our strong industry relationships
Prospector leverages a long history in the plastics industry to help you. Take advantage by attending Webinars given by leaders in the plastics industries. Topics range from safety to processing techniques to cutting edge innovations.
WEBINAR
Speeding Up UL Compliance for E&E Products with UL 94 Recognized Color Concentrates

Presented by Avient June 6, 2024 at 3:00 p.m. CEST / 9:00 a.m. EDT Register Now > Consumers and businesses globally recognize the UL mark on electrical and electronic (E&E) products as an assurance of safety and reliability. It demonstrates … Continued
WEBINAR
Ask the Expert Series – Prospector® Hacks for Comparing Materials
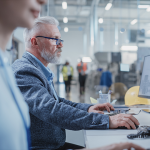
Presented by UL Prospector® May 20, 2024 at 10:30 a.m. EDT Register Now > The fourth session of our Ask the Expert webinar series focuses on how to use Prospector functionality to compare materials. Whether you are an experienced or … Continued
INDUSTRY ARTICLES View more articles

ARTICLE
Material characterization is key to unlocking 3D printing’s full potential
Try building a 3D immersive stereo experience with all monaural components. The result is likely to be suboptimal. A similar challenge is facing developers of digitally manufactured products. When it comes to selecting materials to deliver the desired properties and … Continued
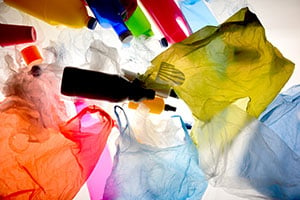
ARTICLE
Plastics – the sustainability challenge
In the article “Polymers in Electric Vehicles” (March 2024), the importance of resource conservation was emphasized. Plastics have inherent properties which make them ideal for modern transport systems; they are light, corrosion-free and easily moulded into complex shapes without the … Continued
Learn from our years of experience
We have 30+ years of expertise in the plastics industry, and we use that knowledge to your advantage. Explore our warehouse of plastics-focused articles in the Prospector Knowledge Center.